KKI invests in advanced additive manufacturing technology
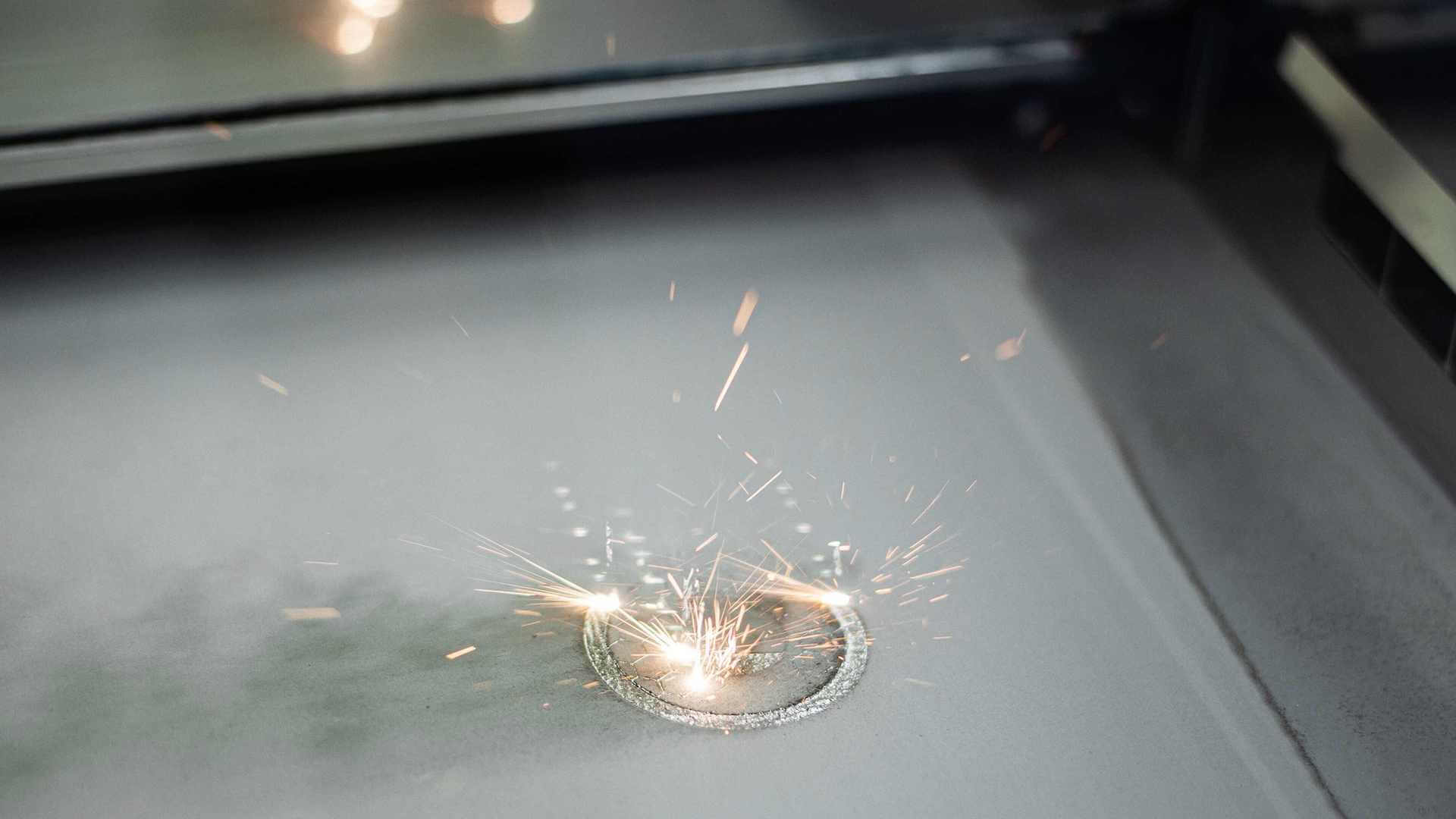
KOSO Kent Introl has taken delivery of a RenAM 500Q Flex additive manufacturing (AM) system at our headquarters in Brighouse, West Yorkshire. We’re investing in next-generation production technologies to understand how we can diversify production and improve sustainability in response to the emerging environmental challenges.
We believe we are the first UK valve business to introduce the technology to the shop floor and are excited of its potential for our customers across all industrial sectors such as the oil and gas industry, mid and downstream, and power sectors. The technology will support our installed base and help us to develop innovative solutions that traditional subtractive machining is too expensive or production prohibitive.
KKI is a global valve engineering leader with our high-quality solutions built to perform in severe service conditions in oil and gas applications. We are investigating the potential for additive manufacturing to meet growing industry demand to adopt innovative technologies, increase energy efficiency, and reduce carbon emissions.
While the technology is in its infancy, it has huge potential, said Matthew Charlton, Technical Director at Kent Introl. “We want to explore how it will enable us, and other manufacturers in the energy sectors, to shift towards more sustainable and efficient manufacturing processes that meet the demand of a rapidly changing market.” In the future, AM could enable KKI engineers or even customers to print replacement parts locally, dramatically reducing the time taken to perform repairs and our carbon footprint.
KKI is one of the first UK businesses to invest in AM technology, but across the world, competition for innovation in this space is increasing. “When some of our larger customers in the industry began requiring additive capabilities, we developed a strategy to invest in AM technology,” Charlton said.
The advanced RenAM 500Q Flex system uses laser powder bed fusion technology to produce components with intricate geometries that are difficult to achieve using traditional manufacturing techniques. It features four 500 W lasers and automated powder handling capabilities to help engineers reduce build time and increase productivity. “Renishaw’s system provided the technical capabilities and support we need — we were also happy to invest in a UK manufacturer,” Charlton said. The system also has additional flexibility that enables users to quickly change metal powders, which can benefit research and development applications for testing different parts.
Initially, the RenAM 500Q Flex system will be used to explore the potential for AM, but in the future could include printing parts. Early investment in AM by KKI is part of a wider push for innovation in the sector. “Current material and quality standards set by the oil and gas industry, for example, by the National Association of Corrosion Engineers (NACE), means that very few manufacturers use AM in this sector,” Charlton said.
KKI believe that this technology has a key place in our future and this RenAM 500Q Flex is just the start of our additive manufacturing journey.